On the road to becoming a true strong country in the field of mold and metal stamping parts, China still needs to make various improvements, which involve various aspects of the current development of the metal stamping parts industry, such as product quality, standardization level, talent supply and demand, product structure, innovation capability, inter enterprise relationships, and the exploration of overseas markets. The first priority is to improve product quality.
At present, the uneven process conditions of automatic lathe parts manufacturers seriously affect the accuracy and quality of automatic lathe parts. For example, in the precision heat treatment process, the different materials of metal stamping parts make it difficult for domestic molds to compete with foreign products in terms of appearance quality and service life. Domestic molds often use 2cr13 and 3cr13, while foreign molds use specialized mold materials, which have superior comprehensive mechanical properties, wear resistance, corrosion resistance, and polishing brightness.
Secondly, the level of standardization needs to be improved. The standardization work of Chinese molds (European standard pins) started late, and the production, sales, promotion, and application of standard parts are relatively backward. Currently, the usage coverage of mold standard parts (Chinese standard pins) is about 40% to 45%, while internationally it is generally higher than 79%, and for small and medium-sized molds it is even higher than 80%.
The dilemma of demand for metal stamping parts processing talents far exceeding supply urgently needs to be improved. The cultivation of talents in the processing of metal stamping parts is a long-term process that requires years of accumulated experience. Due to limitations in software and hardware facilities, some professional students trained by universities lack practical skills; At the same time, the lack of standardized vocational teaching standards has led to uneven quality of students in various training courses in society.
We need to continue to work hard and accelerate the pace of adjusting the structure of power pin products. The overall development direction will still be to achieve a development speed higher than the industry's overall speed for large, precision, complex, and long-life molds and mold standard parts; Continue to increase the proportion of plastic and metal stamping; Expand the number and capabilities of professional die-casting mold manufacturers.
Increase investment to enhance innovation capabilities. It is necessary for backbone enterprises to equip themselves with hardware pins ranging from rough machining and heat treatment of molds to various American standard pins, Australian standard pins, Korean standard pins, and British standard pins. General enterprises should also have CNC machining equipment to achieve fully automatic processing of mold manufacturing. And strengthen innovation through promoting industry university research cooperation.
Promoting joint restructuring among mold enterprises should become the trend. This is mainly due to the fact that a considerable part of the current mold enterprises are private enterprises, objectively facing the problem of difficulty in importing advanced mold making technology and equipment, which undoubtedly intensifies competition in the middle and low-end markets.
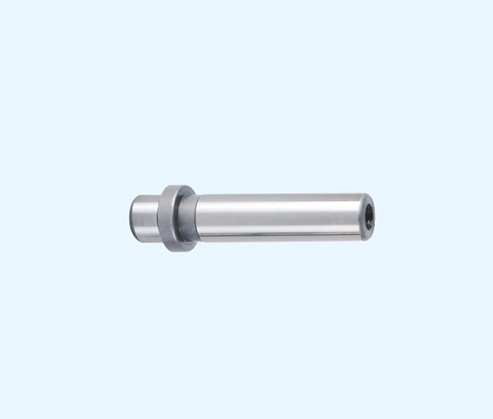