Arrangement:
The hardware mold processing industry is developing rapidly, and the competitive pressure for enterprises is also increasing day by day. Whether in processing technology or processing quality, they are constantly improving and innovating. In this fiercely competitive era, enterprises can only meet customer needs and win the market by ensuring good quality, good service, and continuous innovation capabilities.
1. Bottom processing, guaranteed processing quantity;
2. Alignment of casting blank benchmark, inspection of 2D and 3D surface allowance;
3.2D, 3D surface rough machining, non installation and non working plane machining (including safety platform surface, buffer installation surface, pressure plate surface, side reference surface);
Before semi precision machining, the correct accuracy of the side reference surface must be found;
5. Semi precision machining of 2D and 3D surfaces, precision machining of various installation work surfaces (including limit block installation surfaces and contact surfaces, insert block installation surfaces and back surfaces, punch installation surfaces, waste cutting tool installation surfaces and back surfaces, spring installation surfaces and contact surfaces, various stroke limit work surfaces, wedge installation surfaces and back surfaces), semi precision machining of various guide surfaces and guide holes, leaving a margin for precision machining process reference holes and height reference surfaces, and recording data;
6. Check and recheck the machining accuracy;
7. Clamping and inlaying process;
8. Before precision machining, align the process reference hole reference surface and check the remaining allowance of the embedded block;
9. Precision machining of 2D and 3D surfaces, side punch surfaces and hole positions, precision mold machining process reference holes and height references, precision machining guide surfaces and guide holes;
10. Check and recheck the machining accuracy of hardware molds.
matters needing attention:
1. The process preparation should be concise and expressed in detail, and the processing content should be expressed numerically as much as possible;
2. In the key and difficult areas of processing, special emphasis should be placed on the craftsmanship;
3. It is necessary to combine processing areas and express the process clearly;
When the inlay needs to be processed separately, pay attention to the process requirements for processing accuracy;
5. For the embedded parts that need to be processed separately after combination processing, the benchmark requirements for process installation and separate processing should be met during combination processing;
In mold processing, springs are the most easily damaged, so it is necessary to choose mold springs with long fatigue life.
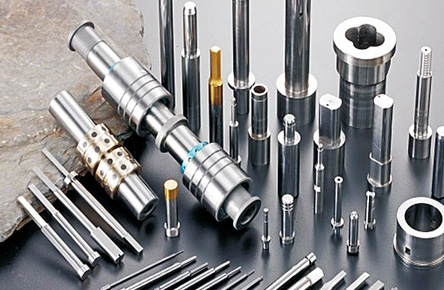