In addition to requiring sufficient strength and toughness during operation, the surface properties of hardware mold accessories are crucial for the working performance and service life of precision mold accessories. The improvement of these properties solely relying on the improvement and enhancement of the matrix material is very limited and uneconomical. However, through surface treatment technology, it is often possible to achieve twice the result with half the effort, which is also the reason for the rapid development of surface treatment technology. Mold polishing technology is an important component of mold surface engineering and a crucial post-treatment process in mold manufacturing. Due to certain problems in domestic polishing technology and materials, a large part of injection molds with high transparency requirements such as point and shoot camera lens injection molds, CD, VCD discs, and tools still rely on imports.
Mirror mold materials are not only a matter of chemical composition, but also require a series of advanced processes such as vacuum degassing, argon gas protection for ingots, vertical continuous casting and rolling, and flexible forging during smelting, which make mirror mold steel have a series of advantages such as fewer internal defects, fine impurity particle size, high dispersion degree, fine metal grain size, and good uniformity, in order to achieve the requirements of polished mirror mold steel. The surface treatment technology of mold accessories is a systematic engineering that changes the morphology, chemical composition, microstructure, and stress state of the surface of precision mold accessories through surface coating, surface modification, or composite treatment technology to obtain the required surface properties. The nitriding process includes gas nitriding, ion nitriding, liquid nitriding, and other methods. In each nitriding method, there are several nitriding techniques that can adapt to the requirements of different steel grades and workpieces. From the perspective of surface treatment methods, they can be divided into chemical methods, physical methods, physicochemical methods, and mechanical methods.
It is worth noting that the polishing of mold surfaces is not only influenced by polishing equipment and process technology, but also by the mirror finish of mold materials. This has not received sufficient attention, which means that polishing itself is constrained by mold materials. Although new processing technologies aimed at improving the surface performance of precision mold components continue to emerge, the main applications in the manufacturing of precision mold components are nitriding, carburizing, and hardening film deposition. Due to the excellent performance of the surface formed by nitriding technology, and the good coordination between nitriding process and quenching process of precision mold parts steel, as well as the low nitriding temperature, there is no need for intense cooling after nitriding, and the deformation of precision mold parts is extremely small. Therefore, nitriding technology was adopted earlier and is also the most widely used for surface strengthening of precision mold parts.
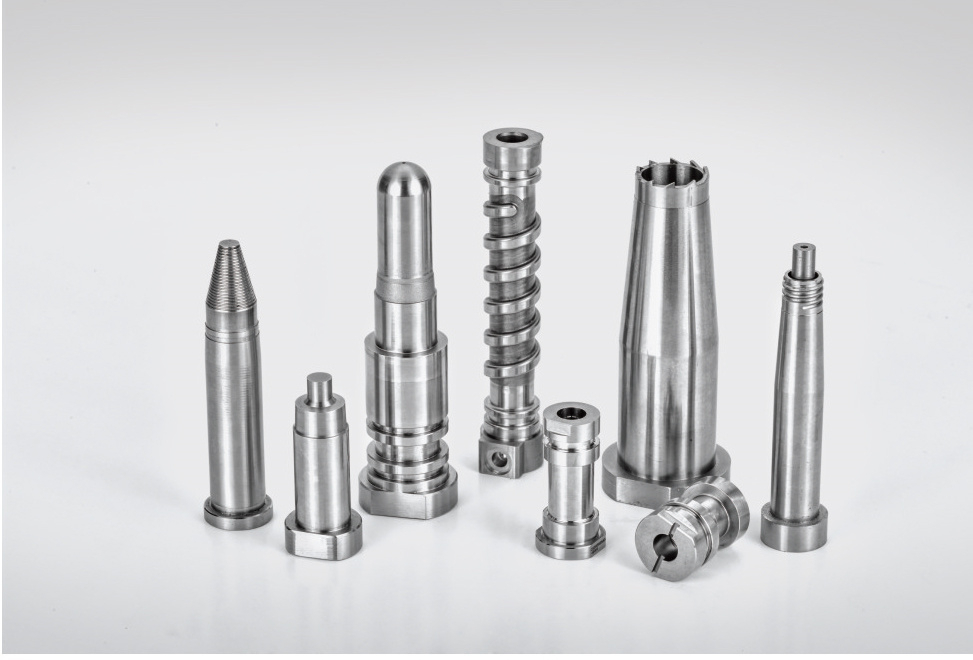