The annual maintenance program required for each injection molding position of the mold depends on different mold cycle periods. Here are some maintenance techniques for mold accessories that can be used by each mold user to ensure the effective operation of mold components such as hot runners, heaters, guide posts and ejector pins, molding inserts, etc., in order to prevent unexpected situations from occurring.
1. Check for any warning signs of rust or moisture at the air vents. If you find rust or moisture near the hot runner exhaust hole, it means internal condensation or the possibility of water pipe rupture. Moisture can cause a fatal short circuit to the heater. If the machine does not run continuously throughout the year and needs to be shut down at night or on weekends, the probability of this condensation phenomenon will increase.
2. Remember to remind the operator not to "clean" the hot nozzle at the gate. If the operator happens to see a small piece of stainless steel at the mold nozzle, it may be a point nozzle component. Cleaning up this seemingly obstructive thing often ruins the hot mouth. To avoid damaging the hot nozzle, please confirm the nozzle type of the hot runner system before taking action and ensure that all operators are well-trained and able to identify the different types of nozzles they come into contact with.
3. Sliding buckle. For machines that run continuously throughout the year, this task should be performed once a week. And the end of the year is a great time to perform a routine lubrication and maintenance on these parts.
4. Interactively verify the resistance value of the heater. You should have already measured the resistance value of the heater when you first started using it, and at the end of the year it is time to measure and compare it again. If the resistance value fluctuates by ± 10%, the heater should be replaced to ensure that it does not malfunction at critical moments in the production process. If the initial resistance value has never been measured before, measure it now and use the obtained value as reference data for future inspections of the heater.
5. Check for signs of wear on the guide post and guide sleeve. Search for any scratches or abrasions, as the wear of these mold components is caused by a lack of lubrication. If the traces are just beginning to appear, you can also extend their lifespan by adding lubricant to the guide post and guide sleeve. If the wear is already severe, then it is time to replace the parts with new ones. Otherwise, the cavity and core parts may not fit well, resulting in uneven thickness of the component cavity wall.
6. Check the water flow condition. Connect a hose at the outlet of the waterway to allow water to pass through the pipe and remain in the bucket. If the water flowing out is not clear or has a color, rust may occur, and if the water flow is not smooth, it means that there is a blockage somewhere. If these issues are found, drill through all the water pipes again (or use any of your most commonly used methods to clean them) to ensure smooth flow. Improving the water treatment system in the factory can prevent various problems caused by rust and blockage in the future.
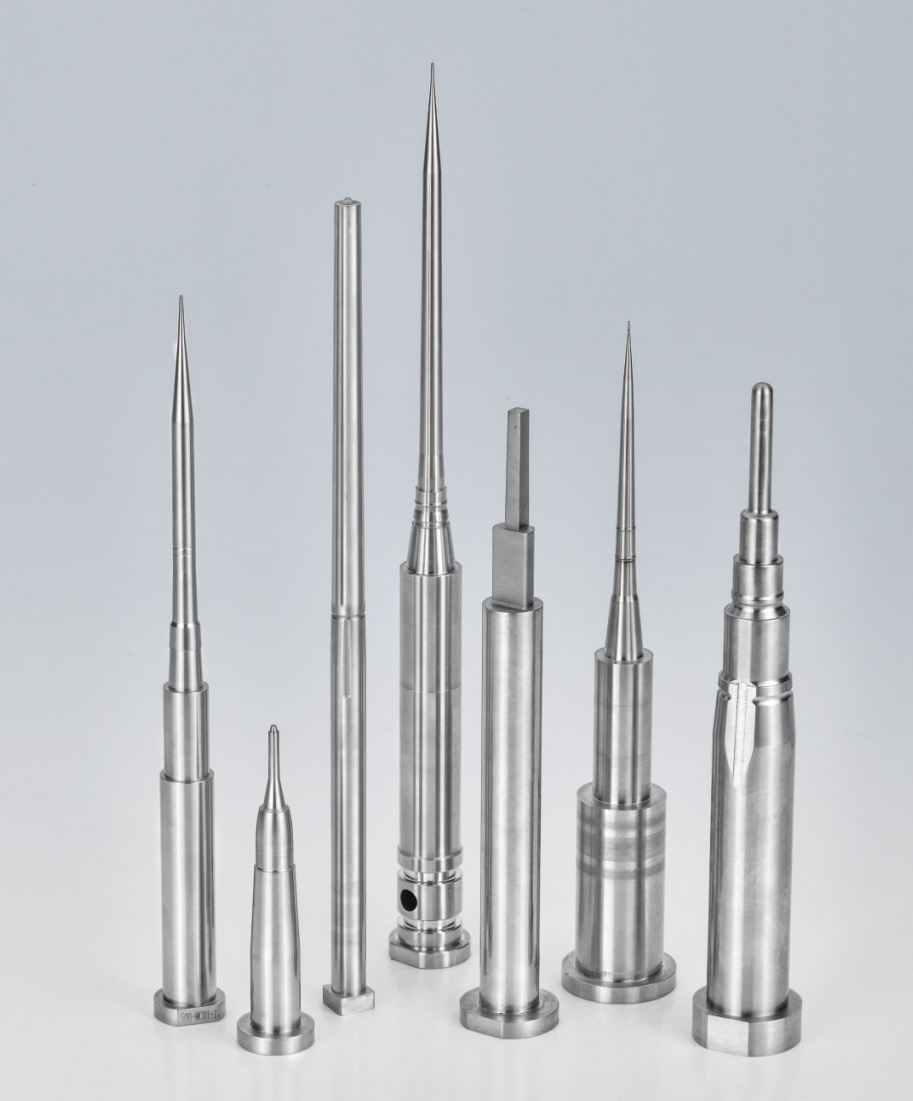